The discovery of steel transformed the course of human civilisation. The stone age ended with the invention and widespread use of copper smelting and alloying copper with other elements, thus introducing metalworking, new and more durable agricultural implements, the development of culture, trade, and governments, and new weapons of war. When heated, copper turns to liquid, after which it can be moulded into a desired shape. When the mould is cooled, the metal returns to its original solid state, this time in the mould’s shape.
Iron replaced copper and tin in the iron age, but it also did something neither metal could: dissolve carbon. If iron is heated and cooled repeatedly, such that the dissolved carbon is removed until a small amount remains, the powerful iron-carbon alloy known as steel is born. Unlike copper or tin, or even iron, steel is hard — and this made all the difference.
As the economist Yanis Varoufakis wrote in his new book, Technofeudalism: What Killed Capitalism: “The swords of their ironclad enemies sliced through their bronze shields, their ploughs failed to cultivate the less fertile soils, the metal braces holding together their dams and temples were too weak to fulfil the ambitions of forward-thinking architects. In contrast, communities that mustered the techne, the art, of ‘steeling’ iron thrived in the fields, on the battlefields, at sea, in commerce, in the arts.”
If only the people of the bronze age had kept heating copper while straining it greatly, they’d have come across a form of the metal that could rival steel.
Deformation and strain rate
A pair of researchers, from the Massachusetts Institute of Technology and Northwestern University, both in the U.S., has reported in a study that when pure copper is heated and also subjected to an extreme strain rate, it behaves like a much harder material would. They attribute this counterintuitive behaviour to new “strengthening mechanisms” that are activated in the material by the higher strain rate. The study was published in the journal Nature on May 22.
“The findings could give rise to new strategies for designing devices to use in extreme conditions like high-speed manufacturing or aerospace engineering, where high temperatures and strain rates are common,” according to a video released by Nature to accompany the paper.
Scientists have already subjected many materials to high strain rates and studied their properties in detail. In the new study, the researchers breached new ground by imparting an even greater strain rate using cutting-edge material-testing technologies.
Strain is how much a material deforms when stress is applied. Say you have a cuboidal ingot of iron and you try to push on one of its sides to change its shape into a solid parallelogram. The extent of deformation — i.e. how slanted the parallelogram is — for a given amount of force will be the strain the ingot is experiencing. A steel ingot is stronger and will require a lot more stress to achieve the same amount of strain. Those of copper or iron will require less.
Strain rate measures the rate at which strain changes. Its unit is (metres per second) per metre, effectively per second. Materials scientists know that when a pure metal is heated, it becomes softer, and they know this to be true when the material is strained anywhere between 0.000001/s and 10,000/s.
Sources of strength
In their study, the researchers — Ian Dowding and Christopher Schuh — accelerated aluminium oxide microparticles using lasers and shot them at a copper substrate at around 860 km/hr. The use of such small stressors prevented the formation of shockwaves, which would have disrupted the material’s structures too much for the changes to be measurable. They tracked the particles’ path using high-speed cameras and, after each impact, measured the minuscule crater that formed. And they repeated these tests at three temperatures: 20, 100, and 177 degrees C.
In their paper, they reported that “as the temperature is increased, the impact crater depth and width decrease”, meaning the copper was behaving at the impact spot like a harder material. Note that the hardness is restricted to the neighbourhood of the impact even if the whole material is maintained at that temperature.
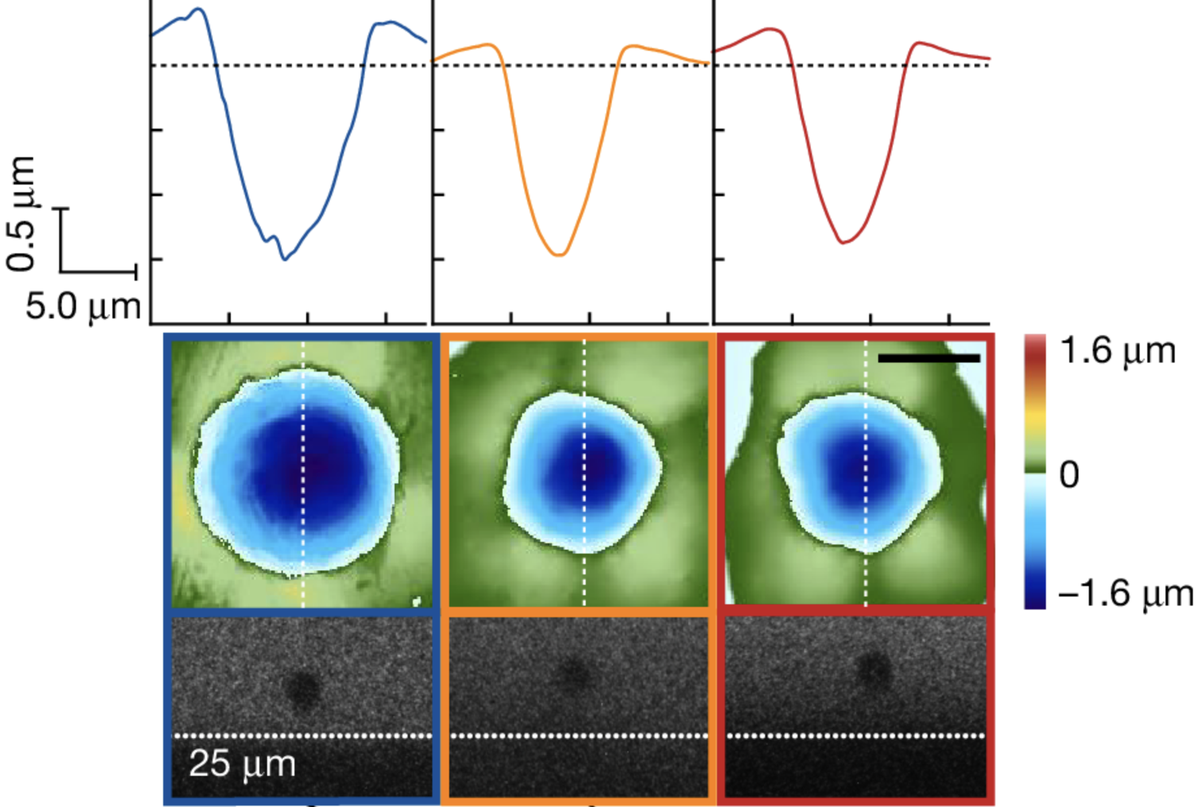
The impact and rebound trajectories of three alumina particles impacting a copper substrate at 20 degrees C (blue), 100 degrees C (orange), and 177 degrees C (red). As the temperature is increased, the rebound velocity of the impacting particle increases, and the crater depth and width decrease.
| Photo Credit:
Dowding, I., Schuh, C.A. Metals strengthen with increasing temperature at extreme strain rates. Nature (2024).
As an alumina bullet strikes the metal at a high velocity, it rapidly deforms the metal at the site of impact, inducing an ultra-high strain of around 10 million /s. This brutal imposition forces the material to respond — and how it responds is controlled by how the material’s strength is organised.
The copper in the researchers’ test had three sources of strength: drag-strengthening, thermal, and athermal. The purpose of each source is to prevent a particular dislocation from propagating through the material. Drag-strengthening refers to interactions between parts of the material dislocated by a stress and vibrational energy in the atomic lattice. Thermal strength refers to the kinetic energy of the atoms in the lattice and their ability to suppress the effects of certain defects in the material. Athermal strength refers to barriers to dislocation other than the atoms’ kinetic energy, such as the interface between two crystal structures (if different parts of the copper object have differently oriented crystal structures).
The strength inventory changes
According to the MIT researchers, when the temperature of the copper object was increased while the strain rate was 10 million /s, the contributions of thermal and athermal strength dropped — but the contribution of drag-strengthening increased so much that the overall strength of the material also increased. At strain rates lower than 1 million /s, the thermal and athermal sources of strength dominated, so as the temperature was increased, the copper became softer.
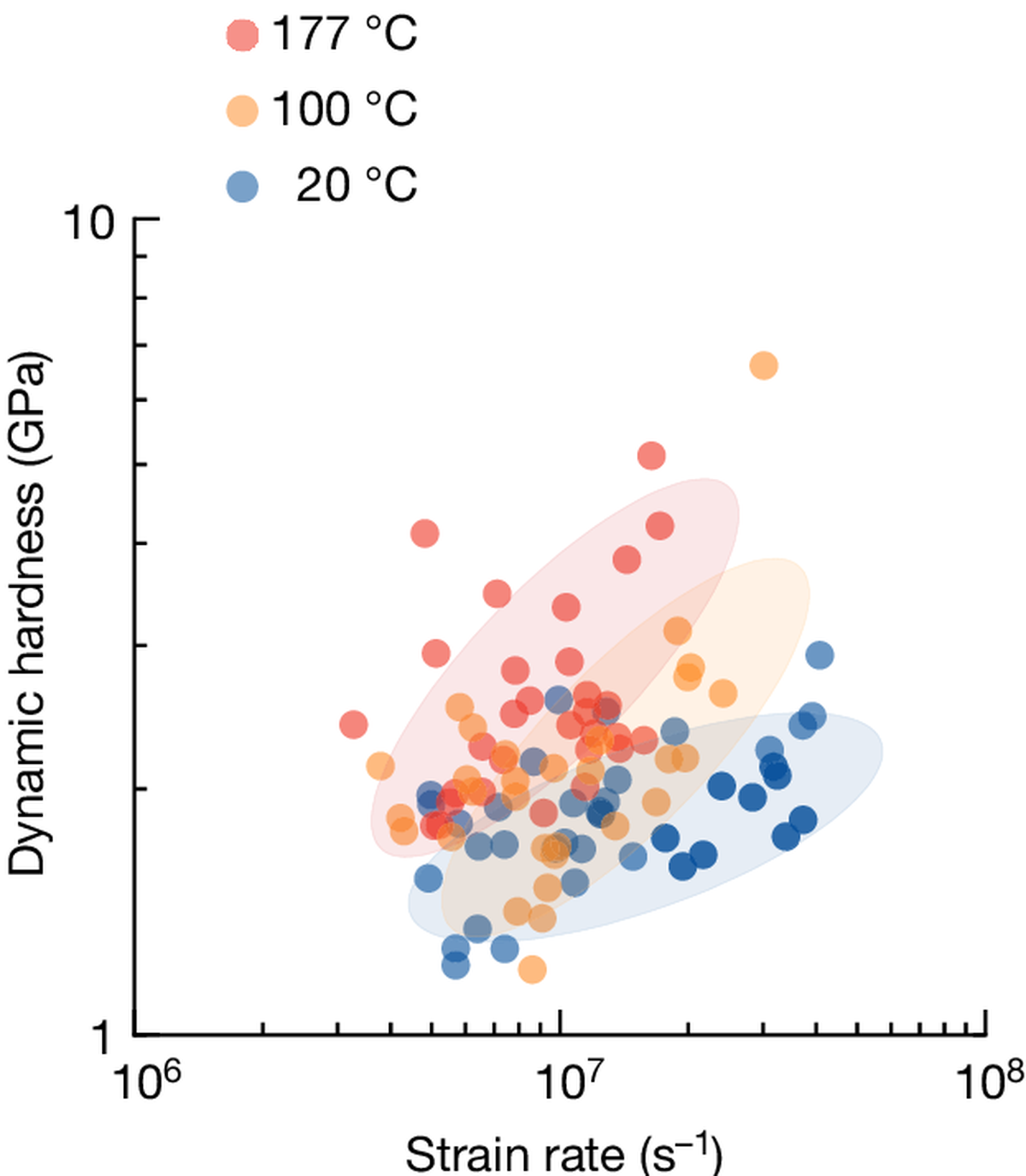
Dynamic hardness measurements from each impact are plotted against deformation strain rate. The shaded regions serve as a guide for the eye to show where most of the hardness values fall for each temperature.
| Photo Credit:
Dowding, I., Schuh, C.A. Metals strengthen with increasing temperature at extreme strain rates. Nature (2024).
The result, to quote from the paper: “although pure copper is a soft metal at low strain rates and would normally be expected to soften at high temperatures, the strength of copper measured here at 10,000,000 / s and 177º C is more than 300 MPa; this is comparable with the conventional strength of 304 steel at this temperature.” (SAE 304 steel is the most common form of stainless steel today.)
The researchers also reported similar effects with pure titanium and gold.
Since the bronze age, metals have penetrated almost all walks of life — from cookware to spaceflight, from office stationery to weapons of mass destruction. In many of these applications, they need to withstand sudden, intense impacts (either from other components from the system they’re part of or external stressors). Materials scientists thus engineer these metals in order to achieve a specific ‘strength inventory’: i.e. to have sources of strength that will resist different kinds of deformation in different operating conditions.
The new study throws a spanner in this thinking by revealing a change in the material’s strength response above a strain rate of around 1 million /s. Even at room temperature (20 degrees C), for example, the study found that the copper substrate had four-times more dynamic strength under a strain rate of 1 million /s than without any strain.
The author is a mechanical engineer by training.